Lean Management im medizinischen Labor: Mehr Qualität und Effizienz
DOI: https://doi.org/10.47184/td.2022.01.01Eine zu lange Turnaround Time gilt als Hauptgrund für einen Laborwechsel. Die Wertstromanalyse ist als Instrument des Lean Managements eine wertvolle Methode, um eine Optimierung der Prozesse herbeizuführen. Die Erkenntnisse aus der Analyse können in konsequente Maßnahmen umgesetzt und so die Turnaround Time wesentlich verbessert werden.
Schlüsselwörter: Probenfluss, Wartezeiten, Probentransport, Schnittstellen, Rüstzeiten
Die Ansprüche an Qualität und Effizienz im medizinischen Labor steigen stetig und in Ausnahmesituationen wie der Corona-Pandemie treten potenzielle Qualitäts- und Effizienzprobleme im Labor deutlich zutage. Gleichzeitig liegt ein chronischer Mangel an Ressourcen vor: Es wird immer schwieriger, qualifiziertes Fachpersonal zu gewinnen, die verfügbaren finanziellen Mittel werden knapper und regulatorische Vorgaben bringen weitere Anforderungen mit sich, die unmittelbare Auswirkung auf die Arbeit in den Laboren haben.
Es wird also in Zukunft mehr denn je darum gehen, die verfügbaren Ressourcen möglichst effektiv einzusetzen, um auch weiterhin die Leistungen der Laboratoriumsmedizin auf höchstem medizinischen Niveau anbieten zu können.
Im folgenden Artikel soll dargestellt werden, wie die Methoden des Lean Managements zur Qualitäts- und Effizienzsteigerung im Labor genutzt werden können.
Key Performance Indicator TAT
Die Turnaround Time (TAT) ist definiert als Zeitdauer von der Auftragserstellung bis zum Zeitpunkt, an dem der Kunde das Ergebnis der Analyse erhält [1]. Für die Kürze oder Länge der TAT sind definierte Prozessschritte maßgeblich (Abb. 1) [2].
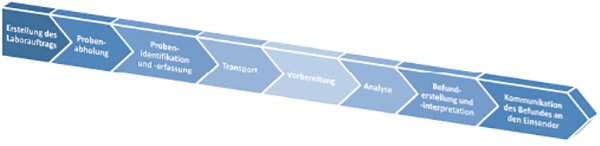
Abb. 1: Prozessschritte der Probenbearbeitung im medizinischen Labor.
Die Unzufriedenheit des Kunden mit der TAT stellt nach wie vor einen der häufigsten Gründe zur Beschwerde dar. Trotz deutlicher Verbesserungen der technischen Ausstattung, der Automatisierung sowie der Digitalisierung der Kommunikation gilt eine aus Kundensicht zu lange TAT als Hauptgrund für einen Laborwechsel.
Es muss demnach das Interesse jedes Laborbetreibers sein, unter Wahrung der höchstmöglichen Qualität der Analyse eine kürzestmögliche TAT zu erzielen. Hierzu müssen Schwachstellen in den Prozessschritten (Abb. 1) identifiziert und geeignete Methoden zur Optimierung eingesetzt werden [3].
Umsetzung
Zur Umsetzung des Lean Managements im Labor muss sichergestellt werden, dass die im Kasten auf S. 14 aufgeführten positiven Einflussfaktoren vorliegen bzw. realisierbar sind. Es macht wenig Sinn, einen Veränderungsprozess zu initiieren, wenn das Top-Management keinerlei Interesse daran hat, ein solches Projekt zu unterstützen bzw. keine Notwendigkeit zur Optimierung sieht. Ebenso muss ein realistischer Projektplan unter Berücksichtigung der zeitlichen Dimension sowie der erforderlichen Ressourcen (Projektteam etc.) aufgestellt werden.
Wie in allen übrigen Bereichen der Medizin steht auch hier vor der Therapie die Diagnostik: Im Folgenden soll dargestellt werden, wie die Wertstromanalyse als Instrument des Lean Managements genutzt wurde, um eine Prozessoptimierung in Laboren der amedes-Gruppe herbeizuführen, und welche Ergebnisse im Hinblick auf die TAT durch konsequente Umsetzung der Erkenntnisse, die aus der Wertstromanalyse gewonnen wurden, erzielt werden konnten.
Wertstromanalyse
In medizinischen Laboren wird in den meisten Fällen ein breites Analyse-Spektrum angeboten. Je nach Anforderung des Einsenders und der im Labor angewandten Methodik werden unterschiedliche Einzelprozesse und Tätigkeiten durchlaufen, die in Summe zu einer komplexen Prozesslandschaft führen. Mit der Wertstromanalyse können derartig komplexe Umgebungen ganzheitlich betrachtet und optimiert werden. Ziel dieses Instruments ist es, den Verschwendungs- und Wertschöpfungsanteil der einzelnen Prozesse zu identifizieren, transparent darzustellen sowie zahlen- und mengenmäßig abzubilden.
Konkretes Vorgehen
Zunächst muss der sogenannte Wertstrom abgegrenzt werden. Den Ausgangspunkt bildet hierbei der Zielparameter „Befundlaufzeit“.
Am Beispiel der amedes-Gruppe wurden sämtliche Tätigkeiten und Aktivitäten, die der Befunderstellung dienen, zu einem Wertstrom gebündelt. Unter anderem umfasste dies die Prozesse von der Probenannahme, Prä- und Routineanalytik über Abläufe der technischen und medizinischen Validierung bis hin zur Befunderstellung und Probenarchivierung.
Im nächsten Schritt wird der Ist-Zustand des Wertstroms abgebildet. Hierzu wurden die einzelnen Prozesse in der Tagesroutine begleitet aufgenommen und transparent dokumentiert. Diese Visualisierung erfolgte standardmäßig in einer eigenen Symbolik mit einzelnen Prozess- und Datenboxen, die als Ergebnis den Material- und Informationsfluss darstellen (Abb. 2).
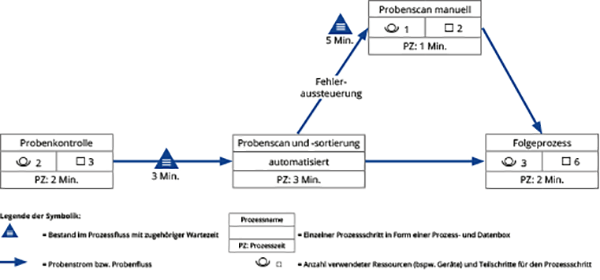
Abb. 2: Schematische Darstellung des Vorgehens zur Wertstromanalyse.
Darüber hinaus wurden zu einzelnen Tätigkeiten Durchlaufzeiten, Prozess- und Wartezeiten sowie eingesetzte Ressourcen (u. a. Personal) erfasst. Dies erfolgte durch strukturierte Beobachtungen, Datenanalysen sowie Befragungen einzelner Fachleute und Prozessverantwortlicher. Weiterhin wurden Zeit- und Fehlerdatensätze aus den jeweiligen Analysegeräten und den Laborinformationssystemen extrahiert sowie gegebenenfalls Probenbestände im Labor erhoben.
Im finalen Methodenschritt wird der erstellte Ist-Wertstrom auf Schwachstellen und Verluste hin untersucht. Als Basis für diese Betrachtung dienen im Lean Management bestimmte Arten von Verschwendungen. Exemplarisch zählen Transporte, Warteschritte oder Nacharbeiten zu diesen Verschwendungsarten in einem Wertstrom und tragen nicht zur Wertschöpfung einer Dienstleistung bei.
Im Anschluss an diese Schwachstellenbetrachtung werden Maßnahmen zur Reduzierung von Verschwendung abgeleitet, sodass ein möglichst verlustarmer Soll-Wertstrom mit einer deutlich verbesserten Durchlaufzeit entsteht.
Erkenntnisse aus den Analysen
Die durchgeführten Wertstromanalysen zeigten aus der Perspektive des Lean Managements vor allem Prozessineffizienzen und Schwachstellenfelder in folgenden Bereichen auf (s. Kasten unten):
a) Bestände und Wartezeiten im Probenfluss
b) Transporte und Bewegung im Laborlayout
c) Wartezeiten bei technischen Geräten und suboptimale Systemeinstellungen
d) Komplexität der Schnittstellen- und Arbeitsprozesse
e) Rüstvorbereitungen von Geräten und Prozessen
Diese wurden durch gezielte Maßnahmen behoben, was sich deutlich auf die Durchlaufzeiten auswirkte (Abb. 3).
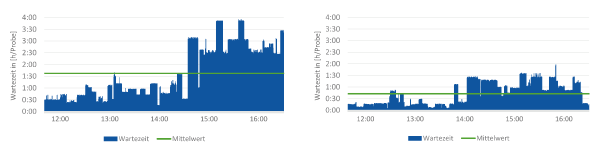
Abb. 3: Taktzeit in Abhängigkeit zur Ankunftszeit während der Peak-Zeit vor (links) und nach (rechts) gezielten Maßnahmen des Lean Managements.
Bestände und Wartezeiten im Probenfluss
Im Proben- und Materialfluss wurden durch die Analyse verschiedene Bestände in den einzelnen Prozessschritten sichtbar. Bestände sind unter Gesichtspunkten des Lean Managements eine Verschwendungsart, die zu Wartezeiten und dadurch zu verlängerten Durchlaufzeiten führt. Beispielsweise bildeten sich Probenbestände vor bestimmten Geräten oder an den Prozessschnittstellen im Wertstrom. Es wurde u. a. deutlich, dass die übergebenen Probenmengen innerhalb des Wertstroms nicht optimal aufeinander abgestimmt waren.
Unterschiedliche Batchgrößen führten darüber hinaus zu großen Belastungen auf bestimmten Geräten oder an Arbeitsschritten und generierten dementsprechend hohe Zeitverluste in der Bearbeitung.
Transporte und Bewegung im Laborlayout
Es konnten darüber hinaus Schwachstellen durch Transporte und Bewegungen bedingt durch das Laborlayout herausgearbeitet werden. Der Probenfluss wurde durch ungünstige Anordnungen der Analysegeräte oder Arbeitsplätze nicht unterstützt, sodass Proben über längere Wege transportiert oder Prozesse mit zusätzlichen und unnötigen Arbeitsschritten ausgeführt wurden, was wiederum zu einer negativen Auswirkung auf die Durchlaufzeit führte.
Wartezeiten bei Geräten und suboptimale Systemeinstellungen
Die technischen Einstellungen an Analysestraßen sowie im Laborinformationssystem bilden ein weiteres erkanntes Verschwendungsfeld. Für viele Prozessschritte sind heute bereits Automatisierungslösungen im Einsatz, die in vielen Fällen von den Herstellern auf die jeweilige Laborlandschaft ausgelegt werden. Hierbei werden eine ganzheitliche Betrachtung sowie Integration in die bestehenden Arbeitsprozesse und Umgebungen oftmals nur rudimentär vorgenommen.
In den Wertstromanalysen zeigten sich erhöhte Aufwände beispielsweise durch technisch fixierte Prozess- und Warteschleifen sowie eine ungünstige Verteilung von Tests und Wartebereichen unter den Analysegeräten. Ebenso wurde eine gezielt gebündelte Abarbeitung der Proben durch die fehlenden Verknüpfungen der Gerätelandschaft in vielen Bereichen erschwert.
Komplexität der Schnittstellen- und Arbeitsprozesse
Die technischen Möglichkeiten zur Optimierung von Prozessschnittstellen und in den Arbeitsprozessen wurden zum Teil nicht ausgenutzt, sodass manuelle Bearbeitungen und Sonderprozesse mit erhöhtem Zeitbedarf beobachtet werden konnten. Dies führte zu entsprechenden Verzögerungen sowie zur Erhöhung der Komplexität der gesamten Abläufe.
Rüstvorbereitungen von Geräten und Prozessen
Ein weiteres Schwachstellenfeld im Labor bildet das „Rüsten“ der Geräte. Hierunter fallen insbesondere Tätigkeiten zur Vorbereitung von Geräten oder Prozessen, beispielsweise die Durchführung von Qualitätskontrollen für Analysen oder die Material- und Reagenzbestückung.
Die Wertstromanalyse ergab, dass es vereinzelt durch verspätete Bereitstellung oder verlängerte Rüstprozesse zum Zeitverlust gekommen war. Dies hatte den Routine- oder Analysestart und somit die gesamte Befundlaufzeit negativ beeinflusst.
Maßnahmen und Ergebnisse
Basierend auf den Ergebnissen der o. g. Analyse wurden spezifische Maßnahmenpakete zur Reduzierung der beschriebenen Verschwendungspunkte erarbeitet und umgesetzt. Es soll beispielhaft auf einige relevante Aspekte eingegangen werden:
In einem ersten Schritt wurde im gesamten Wertstrom ein kontinuierlicher Probenfluss implementiert. Dazu gehörte u. a. die Harmonisierung der unterschiedlichen Batchgrößen. Dadurch wurde unabhängig vom Probenaufkommen eine kontinuierliche Bearbeitung der Proben ohne Bestandsbildungen ermöglicht.
Des Weiteren konnten die fixierten Warte- und Prozessschleifen in bestimmten Analysegeräten oder im Laborinformationssystem entfernt und „Wartebereiche“ in automatisierten Teststraßen stark reduziert werden. Zudem erfolgte eine Integration einzelner automatisierter Komponenten in ein Gesamtkonzept, was eine bessere Testverteilung und gebündelte Probenbearbeitung ermöglichte.
In einzelnen Fällen kam es zu einer Effizienzsteigerung durch Austausch von Geräten und dadurch zu einer schnelleren Abarbeitung der Proben.
Durch Optimierung der Geräteeinstellung konnten darüber hinaus manuelle Prozesse stark minimiert und Sonder- beziehungsweise Doppelprozesse unterbunden werden.
Für einige Prozesse wurde das „Layout“ dem Probenfluss optimal angepasst. Dadurch konnten Transporte und Bewegungen minimiert werden.
Abschließend erfolgte eine Neuauslegung von Steuerung und Organisation des gesamten Wertstroms anhand bestimmter Zeitparameter und hierauf Anpassung der Aktivitäten, Prozessschnittstellen und Ressourcen.
In Summe führten die o. g. Maßnahmen zu einer deutlichen Reduktion der TAT. Je nachdem welcher Prozess bzw. welche Methode betrachtet wird, betrug die Verringerung der Durchlaufzeit bis zu 60 %.
Fazit
Durch Einsatz der Wertstromanalyse als Tool des Lean Managements lassen sich Schwachstellen im Laborablauf identifizieren und strukturiert beseitigen. Durch Implementierung entsprechender Korrekturmaßnahmen können „Verschwendungen“ deutlich reduziert und die Prozesse effizienter und für den Kunden wertschöpfender organisiert werden. Daraus resultiert nicht nur ein direkter Mehrwert für das Labor durch Einsparung von Ressourcen, sondern vielmehr auch ein unmittelbarer Mehrwert für die Einsender sowie deren Patient:innen durch Verkürzung der Befundlaufzeiten.